Animals come in many shapes and forms. Insects and other arthropods share a common physical attribute. They wear their skeletons on the outside. We call them invertebrates. Humans and other mammals, birds, reptiles, amphibians and fish, called vertebrates, have an internal or endoskeleton. In this blog we explore the fusing of internal skeleton-based biology with external robot-based outer skeletons or exoskeletons to give mobility and strength to humans suffering from catastrophic injuries and diseases that impair mobility.
The Necessity and History of Human Exoskeleton Technology
Our earliest forays into exoskeleton technology had nothing to do with restoring movement to a human suffering from an injury or disease. We began with the goal of protecting warriors in battle as we found ourselves often in conflict with neighbours. An escalating arms race included not just weapons but also defences. We invented shields, breastplates, chain mail, and full body armor to counter increasingly sophisticated weapons.
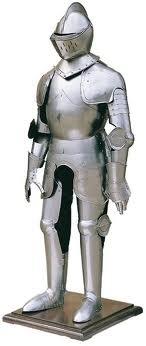
The medieval iron-plated suit, seen above, protected warriors but also encumbered them. When suited and on horseback a warrior was mobile and capable of using lance, mace and broad sword to attack enemies. When out of the saddle a warrior became almost helpless, with walking a chore, let alone fighting.
We have yet to end warfare and our fascination for finding new methods of putting armor on soldiers continues. Today’s army wears synthetic-fibers such as Kevlar, stronger than steel, lighter, and malleable to conform to a body. Soldiers encased in these materials encounter heat stress when worn over a long period because the materials do not breathe. To counter the heat buildup of modern body armor researchers are experimenting with personal cooling systems using phase change materials or PCMs, acting as heat sinks to cool the wearer.
A more recent phase in research is studying how wearable robots can enhance the strength and capability of soldiers. Scientists studying the attributes of arthropod exoskeletons have always been fascinated by the strength exhibited in these animals. For example an ant can carry objects 10 to 50 times its own weight. Could a soldier outfitted with an exoskeleton exhibit similar capability?
Exoskeletons and Military Research
Hardiman, designed by General Electric in 1966, proved to be a balky first attempt at building a powered exoskeleton capable of giving its human operator superhuman strength. Wearing Hardiman (seen below) its operator could lift weights of up to 680 kg. (1,500 lbs).
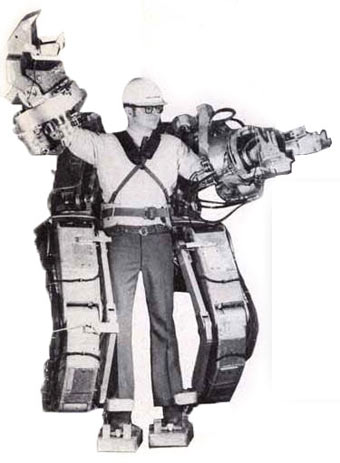
But Hardiman suffered from lots of technical problems. It was heavy, its hydraulics and electro-mechanical systems frequently failed, and it used heavy inefficient batteries.
At about the same time Project PITMAN, out of the Los Alamos Laboratories, began long-term development of an exoskeleton prototype suitable for military field deployment. What the army sought was a powered, armored external apparatus easily worn by a soldier in the field. The suit would feature invulnerability to gunfire and its wearer would be able to easily lift heavy equipment and weapons, and carry wounded soldiers from the field of battle. The suit would give its operator the ability to jump easily and move at a faster than normal human pace.
Research in the last twenty years continues to focus on prototype designs for wearable exoskeletons. One company, Sarcos, recently acquired by Raytheon, has made considerable progress with its XOS robotic suits. The current model, XOS 2 gives its wearer the strength and endurance of two or three soldiers. Consisting of sensors, actuators and controllers, and powered by high-pressure hydraulics, XOS 2 is operator friendly. A wearer can step into it and immediately augment his or her ability to lift 90 kg (200 lbs) repeatedly, and run at a speed of 16 kilometers per hour (10 mph) without tiring. At the same time the wearer climbs ramps and stairs with agility, kicks a soccer ball, handles and passes a basketball, or punches a boxing bag repeatedly without fatigue. The wearer of a XOS 2 can step out at anytime as it waits or operates autonomously on an assigned task.
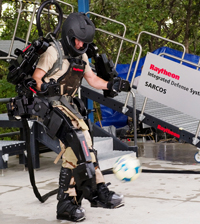
Lockheed Martin is developing HULC(tm), the Human Universal Load Carrier, a lower torso exoskeleton designed to allow soldiers in the field to carry loads of up to 90 kg (200 lbs) for extended periods of time across all types of terrain without feeling fatigue. Click on the link above to see HULC in action. HULC uses a titanium exoskeleton, a computer controller with hydraulics and servomotors, and allows the field operator to snap in modular components such as a lifting frame for hands-free assistance. The wearer can travel at speeds up to 16 kilometers per hour (10 mph). It is easy to put on and take off in battlefield conditions. Currently the lithium-ion battery gives it limited field range. The company is working with Protonex to develop a fuel-cell power source to give it 72 hours of continuous power.
The Biomedical Payoff
Military research in the United States has always led to civilian applications. It is no different when discussing exoskeleton technology. Immediate benefits include enabling people with spinal injuries or neuromuscular diseases to leave their wheelchairs, stand and walk without help.
Ekso Bionics Engineering, a company located in California, is pursuing that goal. Its product, Ekso, offers an escape for wheelchair users through its lower torso exoskeleton. Ekso contains 40 electromechanical servo-motors, operating through intelligent networked software and giving its operator a natural walking gait. An Ekso wearer can sit, stand and walk. At $100,000 the device represents an expensive solution but the company expects the price to decline by half in the near future while it adds many more functions and features. The goal for Ekso is a wearable device that the operator puts on in the morning and uses all day to function in a normal way including going up and down stairs in a home or driving the car to work, or going to a baseball game or a movie at night.
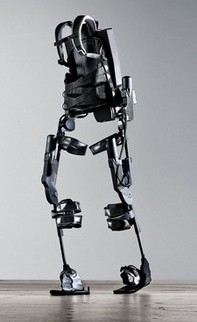
Other companies are pursuing a similar goal. One of them is Cyberdyne, a company headquartered in Tsukuba, Japan, and the creator of the HAL 5 Hybrid Assistive Limb. HAL 5 features a wearable exoskeleton, battery-operated and usable for over 2 hours between recharges. Unlike Ekso, this exoskeleton provides robotic assistance for upper and lower body. HAL 5 takes it cues from nerve signals transmitted from the brain. The wearer controls it by thinking about an action. Sensors attached to the skin pick up the nerve impulses and translate them into movement commands such as standing and walking. The robot’s voluntary control system combines with its autonomous control system to create a full range of movement capability powering both upper and lower limbs.
HAL 5 gives us some insight into exoskeleton design in the near future. Neuroprosthetics that capture electrical signals from the brain will make it possible for seamless integration of exoskeletons with their wearers. As we improve the human-robotic interface we will largely eliminate motor disabilities.